There are only a handful of Autodesk Technology Centers around the world—in the United Kingdom (Birmingham), Canada (Toronto), and the United States (Boston and San Francisco). Each location explores different aspects of the future of making, from construction to advanced manufacturing to artificial intelligence and generative design. And all of the spaces are designed to foster innovation and advance Autodesk’s vision is to help people imagine, design, and make a better world.
Autodesk’s San Francisco location, at Pier 9, serves as a hub for the exploration of the future of manufacturing. Its focus is “configurable microfactories,” also known as iterative manufacturing, and offers a range of advanced manufacturing equipment, robotics, general shop facilities, and workspace to research and develop ideas that push the boundaries of the built environment.
On April 25, the Autodesk Foundation invited Blum Center-affiliated graduate students to meet with Autodesk experts on the future of sustainable design. Fifteen Development Engineering students, InFEWS Fellows, and Big Ideas Hardware for Good participants explored ways to apply their technical skills to the future of manufacturing.
Zoé Bezpalko, who heads Autodesk’s sustainability strategy for the design and manufacturing industries, presented several tools, including CNC machines, 3D printers, woodworking tools, and laser cutters. Autodesk develops the software that runs on these tools and is developing and promoting software solutions and workflows that work either in the design phase, or with these hardware tools, in the manufacturing phase, to reduce material and energy consumption. The result is a reduction in the environmental impact of product design and manufacturing industries.
Bezpalko presented a display of 3D printed objects, including a replica of Van Gogh’s Starry Night and facial sculptures made from paper. A few highly intricate coral replicas caught the attention of several students. Bezpalko explained the coral model was an output from Autodesk Foundation grantee The Hydrous, a startup that uses reality capture and photogrammetry to create high resolution 3D models of coral reefs as part of a multi-pronged conservation effort. Given the severe impacts of climate change on marine ecosystem health, the 3D printed coral reefs help The Hydrous raise awareness and provide ways to collect data, analyze, and monitor coral reefs without the risk of exposing them to further damage.
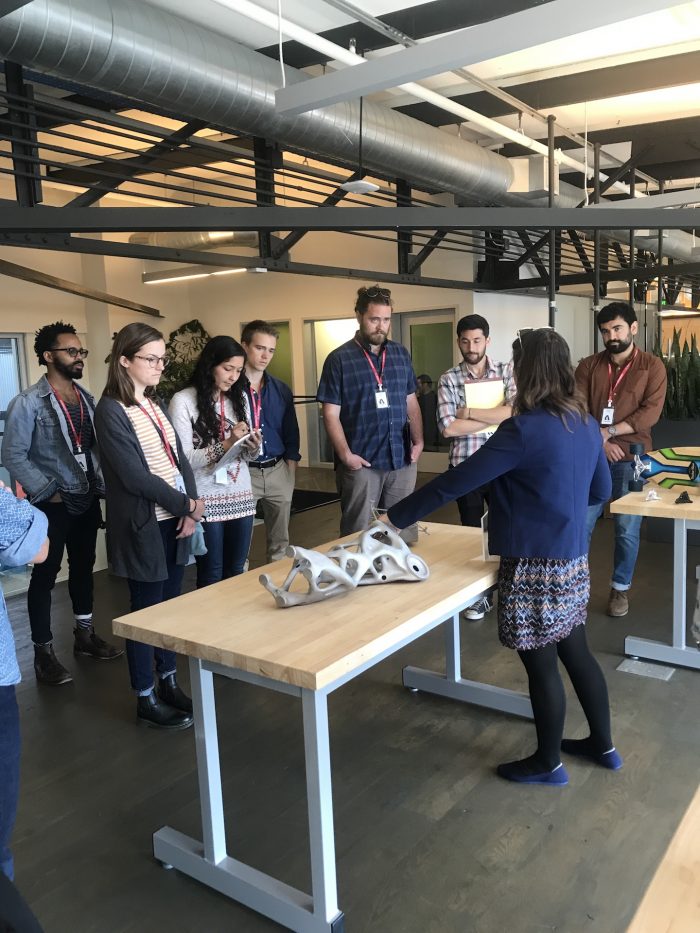
The Blum Center group also visited the robotics lab where two large robotic arms were building a tower from Legos. The group discussed the future of robotics and the many challenges in teaching a robot to complete simple human tasks. Bezpalko showed the group a photo of a 3D printed bridge in Amsterdam, called MX3D, which will soon be installed at one of the city’s oldest and most famous canals. The 3D printed MX3D bridge is a fully functional stainless steel bridge, completed in just six months through robotic additive manufacturing technology.
Over lunch, the group was joined by two senior staff members from Autodesk. The first was Michael Floyd, Autodesk’s AEC Sustainability Strategy Manager, who incubates and promotes novel and existing solutions, largely for high performance buildings, zero-waste construction, and smart, resilient cities. Floyd explained that to decrease the environmental impacts of construction, Autodesk is supporting integration of BIM 360, Autodesk’s building design & construction platform, with EC3, an embodied carbon calculator for buildings. EC3 provides data about the “cradle-to-gate” embodied carbon of locally available building materials, providing data on greenhouse gas emissions associated with raw material extraction, logistics, and manufacturing of specific in-market materials. Green building practices, now widely adopted across the United States and European Union, are still nascent in many developing countries. Floyd hopes that by helping building professionals make informed decisions to minimize the embodied carbon of their projects, Autodesk can catalyze green building practices in the global North, and in developing countries alike.
Morgan Fabian, who leads machine learning research and development for Fusion 360 at Autodesk, talked to the Blum Center group about generative design and how it relates to sustainability. The recent Cal Industrial Engineering graduate explained how the fusion of machine intelligence and creative work can maximize innovative design and function. For example, Autodesk’s Fusion 360 software has generative design capabilities allowing designers to explores alternative design permutations. By providing designers and engineers with a wider array of options, they can select a final design that reduces environmental impact by filtering for specific constraints including materials, cost, and manufacturing methods.
To demonstrate the impact of generative design, Fabian used the example of WHILL, a client that designs and manufactures electric wheelchairs. According to WHILL’s market research, users wanted lighter wheelchairs that are both more affordable and portable. To meet these standards, WHILL used Fusion 360’s generative design capabilities to output dozens of alternative designs that would meet these demands while maintaining the device’s mechanical integrity. The result exceeded expectations; WHILL was able to lighten the frame by more than 30 percent, making it easier to lift and load the wheelchair into the trunk of a car.
George Moore, a UC Berkeley PhD student in Mechanical and Development Engineering, said that the highlight of the Pier 9 visit was learning about Autodesk software to support collaboration and joint decision-making for sustainable design solutions.
Dr. Yael Perez, a researcher at the Blum Center, noted that there are many students like Moore who collaborate with communities, such as the Pinoleville Pomo Nation in northern California, to develop sustainable designs for housing, energy, and education.
“By making software available to students for free, as well as providing other types of supports, Autodesk is bringing local and professional knowledge to the design table for collaborative innovations,” she said.